What is Just-In-Time and how could Brexit affect it?
- What is the Just-In-Time process?
- Why is Just-In-Time used?
- Is Just-In-Time effective?
- Will Brexit affect the use of Just-In-Time by manufacturers?
Have you ever looked at your car and wondered how it’s made?
Making a car is not a small endeavour. Each one is made up of multiple components, from the large, like the engine and chassis, to the small such as spark plugs and light bulbs. All of these parts need to be stored until the point when they’re needed and, large or small, they take up space.
Every business controls their stock differently, from places like Amazon that have warehouses across the globe that cover millions of square feet and are filled with every item you could possibly imagine, to production lines for carmakers like Honda and Nissan in the UK who keep only enough stock on site to make a small number of their end products due to their use of the Just-In-Time process.

In this article we will look into Just-in-Time production, why it’s used by the automotive industry and how Brexit could affect it’s usability in the UK.
What is Just-In-Time?
Just-In-Time, which is also referred to as JIT or the Toyota Production System, is a supply chain process designed to improve efficiency in manufacturing.
JIT can be used within a business reliant on a production line system to:
- Reduce the time a product spends on the production line
- Reduce the time it takes to respond/supply their customers
- Slim down the production process
JIT is a system that ensures the components required for the manufacture of products are delivered ‘in time’ for use. For organisations that require a large number of parts to assemble a single completed product, such as car manufacturers, using JIT is a cost-effective method.
Just-In-Time makes it possible for car manufacturers, and other businesses, to operate with low inventory, removing the necessity for ‘buffer’ stock and large warehouses. These businesses rely, instead, upon the companies in their supply chain delivering the items required to assemble a car when they are required.
Who came up with Just-In-Time?
Just-in-Time was developed in Japan and took over 15-years of trial and error to perfect and become the system that it is today. Taiichi Ohno, at one time a Vice President of Toyota, is credited with the creation of the system, which has been used at the car manufacturer’s factories effectively since the early 1970s. He got his inspiration from the way that American supermarkets keep their shelves stocked; a customer takes what they want from the shelves and buys it and the store then restocks with enough products to fill the space that was left.
How does Just-In-Time work in the car industry?
Just-In-Time works perfectly when it comes to manufacturing cars. It works on the principles of making only what is needed when it’s needed and in the quantity that is needed.
When producing items on a large scale a business wants to avoid waste and using the principles of JIT ensures that this happens.

JIT is an efficient way of making sure that any car that has been ordered is delivered to the customer as soon as possible; the car is built in the shortest period of time that’s feasible. The way that this is achieved is by taking care to follow the guidelines of the Just-In-Time process. There are specific characteristics that identify the JIT process, these include:
- Flow manufacturing – ensuring that machines are used efficiently and making sure that there is continuity in the production process makes the end output possible
- Uninterrupted stream of goods – making sure that there is no delay in the supply of goods and that there are no delays in the process are important
- Collaboration with suppliers – all suppliers have an influence on production and process quality. The success of the process is dependent upon all parties working well together
- Involvement of employees – explaining the process and its importance to employees is vital. Without their buy-in the process will not work properly or efficiently
- Continuous process and quality improvement – JIT can only work successfully if the process is continuously evaluated and all problems managed effectively. Continual monitoring benefits quality and effectiveness.
Thinking about a new car? Contact our team of vehicle experts and they can help you to find the one that meets your needs.
What are the Pros and Cons of Just-In-Time
Every system, no matter how effective or efficient it proves to be, has its positive and negative points. Just-In-Time is no different.
The processes involved in making the system work effectively aren’t for the development of all products or the running of every business.
Pros:
- Lower costs for inventory
- An efficient supply chain can lower costs that can eventually be passed on to the customer
- With needed inventory bought or produced at short notice, storage space requirements are reduced
- Reduced requirement for raw materials lowers production cost and reduces waste
- Improved cash flow – capital expenditure is reduced and the money can be invested in other areas of the business
- Better level of control over the manufacturing process
- Quicker response time when customer needs change
- Less waste, only products that are sold are being produced
- No buffer stock requirement
- Increases savings by reducing waste and warehouse space requirements
- Warehouse space can be repurposed – more assembly lines/retail space
- Makes it possible for more than one model to be assembled on the production line at a time
- More flexible workforce
- Manufacturers will know how many employees are needed at specific parts of the assembly line
- Lower defect rates and costs as quality production can be a focus
Cons:
- There is no room for error if you’re only producing what you need when you need it
- If you don’t have something in stock that a customer has ordered then it means you may be unable to fulfil the order in a timely manner
- Prices – when you are using Just-In-Time you don’t have the luxury of waiting for the best offers on goods you need to complete your orders. When prices of raw materials/components go up, profits go down.
- If one of your suppliers experiences disruption and is unable to deliver their goods to your schedule then the entire production process can be completely shut down.
Just-In-Time is an effective method of managing stock and can ensure that products are manufactured efficiently if the companies in the supply chain are reliable and there are no issues with delivery. However, there are also downsides to the system if there is a breakdown in communication or problems with transport of the raw materials.
How will Brexit affect businesses that use Just-In-Time?
On January 15 2019, Parliament voted against the deal that was proposed by Theresa May, which means that there is a possibility that a no-deal Brexit could become a reality. This could have serious implications for any business that relies upon Just-In-Time.
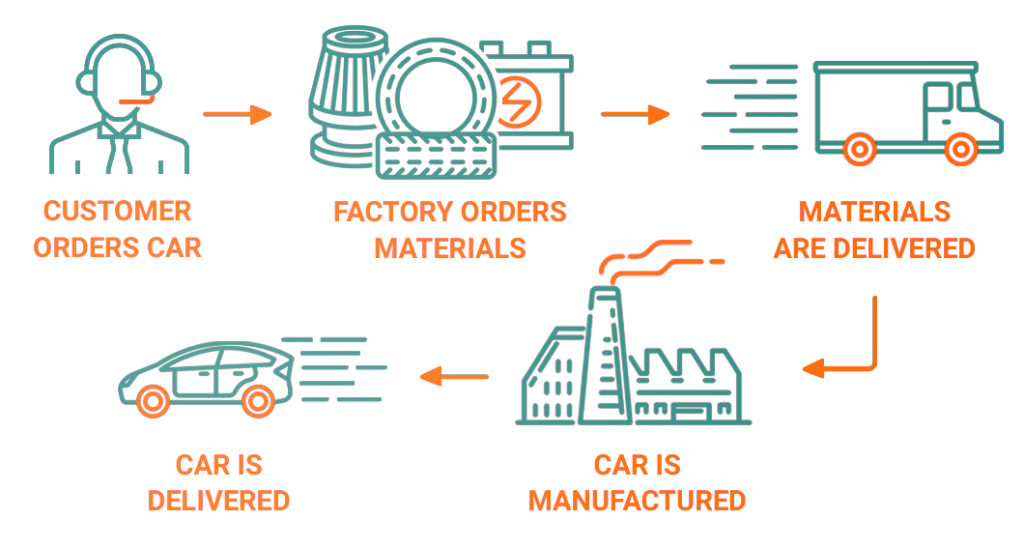
With over 1,100 trucks crossing the Channel daily transporting deliveries intended for car and engine manufacturing plants in the UK, delays at the border could be disastrous for companies that use the JIT process to produce their vehicles. The extra time and staff that businesses could require in order to complete paperwork or delays while goods are checked at Customs could mean that production lines are left empty and customers are left waiting for their cars.
Of course, no decisions have been finalised and in the interim, things carry on as normal.
LOOKING TO GET A NEW VEHICLE?
Contact our team of vehicle specialists and talk to us about your needs. We can help you to find your ideal vehicle. Call us on 01903 538835 or request a callback.
Fed up with looking for your next vehicle?
Need advice from an experienced Vehicle Specialist on what vehicle is right for you?
Book your FREE consultation now